First, the cause of machine tool tap break
1. The quality of the machine tap is not good
Main materials, CNC tool design, heat treatment, machining accuracy, coating quality and more. For example, the difference in size of the transition of the tap section is too large or there is no design transition fillet to cause stress concentration, and it is easy to break at the stress concentration during use.
The cross-section transition at the intersection of the shank and the blade is too close to the weld, resulting in a complex weld stress superimposed on the stress concentration at the cross-section transition, resulting in a large stress concentration, causing the tap to break during use. For example, the heat treatment process is improper. When the tap is heat treated, it may cause cracks in the tap if it is not preheated, quenched or overheated, not tempered in time and cleaned prematurely before quenching. To a large extent, this is also an important reason why the overall performance of domestic taps is not as good as imported taps.
2. improper selection of machine taps
High-quality machine taps, such as cobalt-containing high-speed steel taps, carbide taps, coated taps, etc., should be used for the tappings with too much hardness. In addition, different tap designs are used in different work situations. For example, the number of chips, the size, the angle, etc. of the machine taps have an effect on the chip removal performance.
3. Machine taps do not match the material being machined
This problem has received more and more attention in recent years. In the past, domestic manufacturers always felt that the import was good and the price was good. In fact, it was suitable. As new materials continue to increase and are difficult to machine, the variety of tool materials is constantly increasing to accommodate this need. This requires the selection of a suitable tap product before tapping.
4. The bottom hole diameter is too small
For example, when machining a black metal material M5×0.5 thread, the cutting machine tap should use a 4.5mm diameter drill bit to make the bottom hole. If the 4.2mm drill bit is misused to make the bottom hole, the cutting part of the tap will increase when tapping. Large, which in turn breaks the tap. It is recommended to select the correct bottom hole diameter according to the type of tap and the material of the tapping piece. If the drill bit is not fully matched, you can choose a larger one.
5. Attack material problem: the material of the attack piece is not pure, and the local part has too hard point or air hole, which causes the tap to lose balance and break.
6. The machine tool does not meet the precision requirements of the tap
Machine tools and clamping bodies are also very important, especially for high-quality taps, as long as the machine tool and the clamping body of a certain precision can achieve the performance of the tap. It is common that the concentricity is not enough. At the beginning of tapping, the tap is not positioned correctly, that is, the spindle axis is not concentric with the center line of the bottom hole, and the torque is too large during the tapping process, which is the main reason for the tap break.
7. Cutting fluid, the quality of lubricating oil is not good
Many domestic enterprises have begun to pay attention to it. Many companies that have purchased foreign tools and machine tools have a very deep understanding. The quality of the cutting fluid and lubricating oil is problematic. The quality of the processed products is prone to burrs and other life problems. There will also be a big reduction.
8. Cutting speed and feed rate are unreasonable
When there is a problem in processing, most domestic users are reducing the cutting speed and reducing the feed rate, so that the pushing force of the tap is reduced, and the thread precision of the production is greatly reduced, thereby increasing the roughness of the thread surface, the thread. Aperture and thread accuracy are uncontrolled, and problems such as burrs are of course more inevitable. However, if the feed speed is too fast, the resulting excessive torque will easily cause the tap to break. The cutting speed during machine attack is 6-15m/min for general steel; 5-10m/min for quenched and tempered steel or harder steel; 2-7m/min for stainless steel; and 8-10m/min for cast iron. In the same material, the diameter of the tap is slightly higher, and the diameter of the tap is larger.
9. The skills and skills of the operators do not meet the requirements: All of the above problems require the operator to make judgments or feedback to the technicians, but at present most of the operators in China do not pay enough attention. For example, when machining a blind hole thread, when the tap is about to contact the bottom of the hole, the operator does not realize that the tapping speed is still given when the tap is not reached, or the chip is broken when the chip is not smooth. . It is recommended that operators strengthen their sense of responsibility.
It can be seen from the above that the causes of tap breaks can be varied, such as machine tools, fixtures, workpieces, crafts, chucks and knives, etc., and the real reason may never be found on paper alone. As a qualified and responsible tool application engineer, the most important thing is to go deep into the field, not just imagine. For the simplest example, if the length of the tap cutting cone is too long, it will break when hitting the bottom of the bottom hole during tapping. If you don't go into the field, just guess the tap performance, workpiece material, processing technology, etc.
I couldn't think of dreaming at the beginning, but there are customers who have experienced such problems that you might think are extremely low-level, but you have to face it.
In fact, neither the traditional tapping equipment nor the expensive CNC equipment can solve the above problems in principle. Because the machine does not recognize the tap's working condition and the most appropriate torque required, it will only repeat the machining according to the preset parameters. The failure is only found when the machined part is finally detected with a thread gauge, and it is too late to find it.
Even if it was found, it was useless. The scrapped and expensive parts had to be scrapped, and the unqualified products had to be thrown into the defective products. Therefore, in large enterprises, large-scale, expensive and precise workpiece processing, even if it is expensive to use imported taps, it is not domestically produced, because once the tap is broken, the workpiece is scrapped, and the price paid is quite large. Foreigners are awkward, and the price of taps is high. Whenever a considerable portion of the profits of a company are taken by foreigners, it is not sad. Hey, the Chinese still need to work hard!
Second, the turning of titanium alloy
The thermal conductivity of titanium alloy is very poor, and the contact length between the chip and the tool is very short, which is not conducive to the derivation of cutting heat, so that the temperature in the cutting edge area is high, about twice as high as that of the 45 steel. In addition, the tool wear is also very serious. On the one hand, the chemical affinity of the titanium alloy and the tool material is strong, and it is easy to bond with Ti, Co, C and other elements in the tool material, and the bonding wear is aggravated at high temperature; Alloys are easily combined with oxygen and nitrogen in the air to form a hard, brittle surface that exacerbates tool wear. In addition, since the contact length between the chip and the rake face of the tool is only 1/3 to 1/4 of that when the steel is cut, the cutting force is concentrated near the cutting edge, and the tool is easily chipped. Therefore, cutting tool materials for titanium alloys, such as high-speed steel, should be made of cobalt, aluminum or high vanadium high-speed steel. In order to improve production efficiency, cemented carbide tools should be used as much as possible, but high-strength fine-grained tungsten-cobalt cemented carbides with low affinity and good thermal conductivity should be selected, as shown in Table 1:
Table 1 Tool material selection for turning titanium alloy

In order to improve the cutting edge strength and heat dissipation, a small rake angle and a blade inclination angle should be used. Since the surface elasticity of the machined surface is large when the titanium alloy is cut, the relief angle should take a larger value. The cutting edge should adopt a circular arc transition edge. The cutting edge must not have defects such as burrs, tiny notches or cracks. The roughness of the blade surface should be within Ra0.2μm to ensure smooth chip removal and avoid chipping. The tool geometry parameters for turning titanium alloy are shown in Table 2:
Table 2 Tool geometry selection for turning titanium alloy
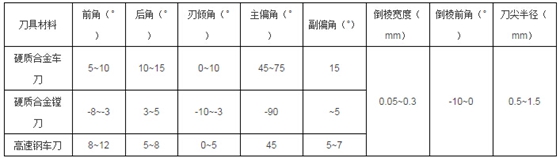
The speed of turning titanium alloy should not be too high, the amount of back knife can be larger, and the feed rate should be appropriate. If the feed rate is too large, it will cause the cutting edge to burn out; if the feed amount is too small, the cutting edge will wear too fast during the work hardening layer. When turning titanium alloy, it can be cooled by rust-proof emulsion or extreme pressure emulsion. The cutting amount selection for turning titanium alloy is shown in Table 3:
Table 3 Selection of cutting amount for turning titanium alloy
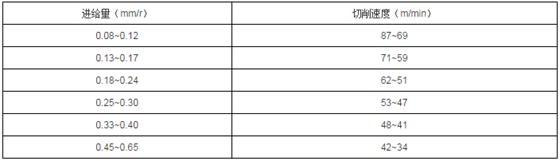
Note: The conditions of use of this table: tool material YG8, workpiece material TC4, tool geometry angle rake angle = 5 °, back angle = 10 °, lead angle = 75 °, declination = 15 °, tip radius = 0.5 mm , cutting depth = 1mm, dry cutting. If a cutting fluid is used, the cutting speed in the table can be appropriately increased.
These beads are coated with a special coating materials, during the manufacture of the glass beads, which will improve the characteristics of moisture-proof and adhesion of glass bead. In the way, the life cycle of the glass beads can be prolonged and this enhances the beads reflectivity in a rainy night. These beads are usually used in white or yellow line-construction of highway.
The glass bead can be produced based on the standard of countries or areas, such as EN1423/1424, AASHTO M247, BS6088, JIS R3301 and KS L2521 etc.
Dual Coated Glass Beads,Dual Coated Glass Beads Roadmarking,Reflective Dual Coated Glass Beads,Dual Coated Glass Beads Traffic Paint
CHIYE GLASS BEAD (HEBEI) CO., LTD , https://www.chiyeglassbeads.com