Chinese name: Epoxy resin English name: epoxy resin Definition: A general term for low molecular weight substances with two or more epoxy groups in the molecule and their crosslinked solidified products. The most important one is bisphenol A type epoxy resin. Applied science: Materials Science and Technology (a subject); Polymer materials (two subjects); Plastics (two subjects)
The above content was approved by the National Science and Technology Terminology Committee.
Help editing encyclopedia business card
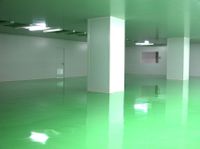
Epoxy mortar floor
Epoxy resin is an organic polymer compound which generally contains two or more epoxy groups in the molecule, and their relative molecular mass is not high except for a few. The molecular structure of the epoxy resin is characterized by the presence of an active epoxy group in the molecular chain, and the epoxy group may be located at the end, in the middle or in a ring structure of the molecular chain. Since the molecular structure contains an active epoxy group, they can be cross-linked with various types of curing agents to form an insoluble, infusible polymer having a three-dimensional network structure.
|
|
Contents Basic introduction Basic classification Physical and chemical properties Production application Usage introduction Classification Detailed use Guide Expand basic introduction Basic classification Physical and chemical properties Production application Usage Introduction Classification Detailed use Guide
Edit this paragraph Basic introduction Basic overview Where the molecular structure contains epoxy groups of polymer compounds are collectively referred to as epoxy resin. The cured epoxy resin has good physical and chemical properties. It has excellent bonding strength to the surface of metal and non-metal materials, good dielectric properties, small set shrinkage, good dimensional stability and high hardness. It has good flexibility and is stable to alkali and most solvents. It is widely used in various departments of national defense and national economy for casting, dipping, laminating, bonding, coating and other purposes.
Domestic research China has been researching epoxy resin since 1958 and has invested in industrial production at a rapid rate. It has been flourishing all over the country, except for the production of ordinary bisphenol A-epichlorohydrin epoxy resin. In addition, various types of new epoxy resins are also produced to meet the urgent needs of national defense construction and various sectors of the national economy. [1]
Edit this paragraph basic classification classification standard epoxy resin classification is not yet unified, generally according to strength, heat resistance grade and characteristics classification, epoxy resin has 16 major varieties, including general rubber, structural adhesive, temperature resistant rubber, low temperature resistance Glue, underwater, wet surface glue, conductive glue, optical glue, spot welding glue, epoxy resin film, styrofoam, strain rubber, soft material bonding glue, sealant, special glue, suspected to be cured There are 16 kinds of civil construction glue.
Several classifications Currently, there are several classifications for epoxy resin adhesives in the industry:
1. According to its main components, it is divided into pure epoxy resin adhesive and modified epoxy resin adhesive;
2. According to its professional use, it is divided into mechanical epoxy resin adhesive, construction epoxy resin adhesive, electronic eye epoxy resin adhesive, repair epoxy resin adhesive, transportation glue, marine glue. Wait;
3. According to the construction conditions, it is divided into room temperature curing type glue, low temperature curing type glue and other curing type glue;
4. According to its packaging form, it can be divided into single-component adhesive, two-component adhesive and multi-component adhesive;
There are other sub-methods, such as solvent-free glue, solvent-based glue and water-based glue. However, there are currently more applications in component classification.
Edit this paragraph physicochemical properties of the material properties of epoxy resin with hydroxyl and epoxy groups, the hydroxyl group can react with isocyanate. The epoxy resin is directly added to the hydroxyl group-containing component of the polyurethane adhesive as a polyol. With this method, only the hydroxyl group participates in the reaction, and the epoxy group fails to react.
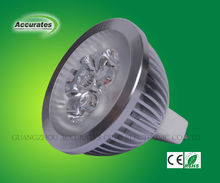
Title
The epoxy is opened by an acidic resin and a carboxyl group, and then reacted with an isocyanate in the polyurethane adhesive. It is also possible to dissolve the epoxy resin in ethyl Acetate , add phosphoric acid to warm the reaction, and add the adduct to the polyurethane adhesive; the initial viscosity of the glue; heat resistance and hydrolytic stability can be improved. The alcoholamine or amine reacts to form a polyol, and the presence of a tertiary nitrogen atom in the adduct accelerates the NCO reaction.
The use of epoxy resin as a polyhydroxy component combines the advantages of polyurethane and epoxy resin, and has good bonding strength and chemical resistance. The epoxy resin used in the manufacture of polyurethane adhesive generally adopts EP-12 and EP-13. , EP-16 and EP-20 and other varieties.
Modification method
1. Select a curing agent;
2. Adding a reactive diluent;
3. Adding a filler;
4. Add another thermosetting or thermoplastic resin;
5. Improve the epoxy resin itself.
Edit this paragraph production application production situation
1.1 Regional distribution of epoxy resin production in the world
The production of epoxy resin is mainly concentrated in China, Japan and Europe. Others include Korea, the United States, Taiwan, Thailand, South Africa and Venezuela. China's production capacity accounts for about 60% of the world's total production capacity.
1.2 Monopoly pattern of world epoxy resin production
The world's epoxy resin production is mainly monopolized by the three giants Shell, Dow and Ciba. In addition, Japan's Dongdu Chemical, Dainippon Ink, Japan Epoxy Resin Manufacturing Co., Ltd., Korea's Guodu Chemical (joint venture with Japan's Dongdu Chemical Co., Ltd.) Several of them are also renowned in the world's epoxy industry for their advanced production processes.
1.3 Domestic epoxy producers
There are more than one hundred epoxy resin manufacturers in China, but most of them except for Yueyang and Wuxi. At present, most of the domestic epoxy resin plants are small in scale, single in variety, equipment is backward, and resin quality is low. At present, Shell, Dow, Ciba and several Japanese companies are stepping up their penetration in China's epoxy consumer market. Manufacturers face extremely serious challenges.
Demand variety
2.1 World Epoxy Resin Grades
At present, the most widely used variety in the world is bisphenol A epoxy, followed by brominated bisphenol A and phenolic epoxy, and other varieties are used in small quantities.
2.2 Domestic Epoxy Consumer Variety
The actual epoxy resin produced in China is only a few grades of bisphenol A type. According to statistics, in 1997 the national demand for epoxy resin was about 110kt, the production volume was about 30kt, and the import volume was about 60kt. Domestic epoxy production varieties are very single, mainly bisphenol A type. Due to the poor quality of domestic epoxy, many high-quality epoxy, such as high-quality liquid epoxy, brominated epoxy, phenolic epoxy, etc., must be imported.
2.3 Distribution of epoxy resin in various industries
Epoxy resins are currently used in the coatings and electronics industries. Epoxy for composite molding (mainly used in printed circuit boards in the electronics industry) accounts for a quarter.
Market Prospects China is the world's largest and last virgin market for epoxy resins. The outlook for China's epoxy market is very broad.
Epoxy coating (anti-corrosion, anti-marine biological pollution). Experts predict that in 2000 China's marine coatings need 40,000 tons, most of which are epoxy anti-corrosion coatings.
The container manufacturing industry continues to develop at a high speed, and can coatings require more and more epoxy resin.
The Northeast region is bound to be a huge potential market for epoxy resins.
Waterborne epoxy coatings are promising. Both are the mainstream of epoxy coating development. China is the fourth largest producer of powder coatings in the world and the largest producer of powder coatings in Asia. The Chinese government has identified powder coatings and waterborne coatings as priority developments in the future, and waterborne epoxy coatings play an important role in the waterborne coatings industry.
Edit this paragraph Use Introduction The usage profile is added and used according to the user recipe.
Storage Introduction This product has stable indoor storage performance at 5°C-35°C for a long time.
Packaging product
Packed in 25 kg plastic drums.
1. Various forms. Various resins, curing agents, and modifier systems can be adapted to the requirements of various applications, ranging from very low viscosity to high melting point solids.
2. Easy to cure. Epoxy resin system can be cured in the temperature range of 0-180 °C by using various curing agents.
3. Strong adhesion. The presence of polar hydroxyl and ether linkages inherent in the epoxy resin molecular chain provides high adhesion to a wide variety of materials. The epoxy resin has low shrinkage when cured, and generates small internal stress, which also contributes to an improvement in adhesion strength.
4. Low shrinkage. The reaction of the epoxy resin and the curing agent used is carried out by a direct addition reaction or a ring-opening polymerization reaction of an epoxy group in a resin molecule, without the release of water or other volatile by-products. They exhibit very low shrinkage (less than 2%) during curing compared to unsaturated polyester resins and phenolic resins.
5. Mechanical properties. The cured epoxy resin system has excellent mechanical properties.
6. Electrical performance. The cured epoxy resin system is an excellent insulating material with high dielectric properties, surface leakage resistance and arc resistance.
7. Chemical stability. Generally, the cured epoxy resin system has excellent alkali resistance, acid resistance, and solvent resistance. Like other properties of cured epoxy systems, chemical stability also depends on the resin and curing agent chosen. Epoxy resin and curing agent can be used appropriately to make it have special chemical stability.
8. Dimensional stability. The combination of many of the above properties gives the epoxy resin system outstanding dimensional stability and durability.
9. Resistant to mold. The cured epoxy resin system is resistant to most molds and can be used in harsh tropical conditions.
Edit this paragraph classification Detailed classification classification According to the molecular structure, epoxy resin can be roughly divided into five categories:
1. Glycidyl ether epoxy resin
2. Glycidyl ester epoxy resin
3. Glycidylamine epoxy resin
4. Linear aliphatic epoxy resin
5. The most widely used epoxy resin in the alicyclic epoxy resin composite material is the above-mentioned first type of glycidyl ether epoxy resin, and among them, the diphenolic propane type epoxy resin (referred to as bisphenol A type). Epoxy resin). This is followed by a glycidylamine epoxy resin.
The glyceryl ether glycidyl ether epoxy resin is obtained by polycondensation of an active hydrogen-containing phenol or Alcohol with epichlorohydrin.
(1) Diphenol-based propane type epoxy resin The diphenol-based propane type epoxy resin is obtained by polycondensation of diphenol-based propane and epichlorohydrin.
Industrial diphenolic propane type epoxy resins are actually mixtures of molecules containing different degrees of polymerization. Most of these molecules are linear structures containing two epoxy end groups. A few molecules may be branched, and a very few molecules terminate in a group that is a chlorohydrin group rather than an epoxy group. Therefore, the epoxy group content and the chlorine content of the epoxy resin have a great influence on the curing of the resin and the properties of the cured product. The industrial control indicators for the resin are as follows:
1 epoxy value. Epoxy value is the most important indicator to identify the properties of epoxy resin. Industrial epoxy resin models are distinguished by different epoxy values. The epoxy value refers to the amount of the epoxy group-containing substance per 100 g of the resin. Multiplying the reciprocal of the epoxy value by 100 is called epoxy equivalent. The meaning of the epoxy equivalent is the number of grams of epoxy resin containing 1 mole of epoxy group.
2 inorganic chlorine content. The chloride ion in the resin can cooperate with the amine curing agent to affect the curing of the resin, and also affect the electrical properties of the cured resin. Therefore, the chlorine content is also an important indicator of the epoxy resin.
3 organic chlorine content. The content of organic chlorine in the resin indicates the content of the part of the chlorohydrin group in the molecule which has not been closed-loop, and its content should be reduced as much as possible, otherwise it will affect the curing of the resin and the properties of the cured product.
4 volatiles.
5 viscosity or softening point.
(2) Phenolic polyepoxy phenolic polyepoxy resin includes phenol formaldehyde type and o-cresol formaldehyde type epoxy resin, which contains more than two in-line molecules compared with diphenol-based propylene type epoxy resin. The epoxy group has a high crosslink density of the product after curing, and has excellent thermal stability, mechanical properties, electrical insulation, water resistance and corrosion resistance. They are formed by polycondensation of a novolac resin and epichlorohydrin.
(3) Other polyhydric phenolic glycidyl ether type epoxy resins The practical representatives of such resins are: resorcinol type epoxy resin, resorcinol-formaldehyde type epoxy resin, tetraphenol B Alkyl epoxy resin and trishydroxyphenylmethane epoxy resin. These polyfunctional glycidyl ether resins have high heat distortion temperature and rigidity after curing.
Or blended with general-purpose E-type resin for use as a base material for high-performance composite materials (ACM), printed wiring boards, etc.
(4) aliphatic polyol glycidyl ether type epoxy resin aliphatic polyol glycidyl ether molecule contains two or more epoxy groups, most of which are low in viscosity; most are long chains Linear molecules are therefore flexible.
Other types (1) glycidyl ester epoxy resin glycidyl ester epoxy resin and diphenolic propane epoxidized resin, it has low viscosity, good processability; high reactivity; adhesive force than universal ring High oxygen resin, good mechanical properties of cured product; good electrical insulation; good weather resistance, and good resistance to ultra-low temperature. Under ultra-low temperature conditions, it still has higher bonding strength than other types of epoxy resin. It has good surface gloss, good light transmission and weather resistance.
(2) Glycidylamine-based epoxy resin The resin has the advantages of high polyfunctionality, high epoxy equivalent, high crosslinking density, and remarkable heat resistance. At present, carbon fiber reinforced composites (CFRP) have been manufactured at home and abroad using the superior adhesion and heat resistance of glycidylamine epoxy resin for aircraft secondary structural materials.
(3) alicyclic epoxy resins, such as epoxy resins, are obtained by epoxidation of double bonds of alicyclic olefins, their molecular structure and diphenolic propane type epoxy resin and other epoxy resins. There is a big difference. The former epoxy groups are directly attached to the alicyclic ring, while the latter epoxy groups are all attached to the benzene nucleus or aliphatic hydrocarbon with a epoxidized propyl ether. The cured product of the alicyclic epoxy resin has the following characteristics: 1 high compression and tensile strength; 2 long-term explosion can maintain good mechanical properties under high temperature conditions; 3 arc resistance, ultraviolet aging resistance and Good weather resistance.
(4) Aliphatic epoxy resin The epoxy resin has no benzene core or alicyclic structure in its molecular structure. There is only a fatty chain, and the epoxy group is connected to the aliphatic chain. The epoxidized polybutadiene resin has good strength, toughness, adhesion, and positive and negative temperature resistance after curing.
Edit this paragraph use guide Basic introduction Epoxy resin and epoxy resin adhesive itself is non-toxic, but due to the addition of solvents and other toxic substances in the preparation process, many epoxy resins are "toxic", in recent years, the domestic epoxy resin industry is The epoxy resin is "non-toxic" in color by means of aqueous modification, avoidance of addition, and the like. Epoxy resins are generally used in conjunction with additives to achieve application value. The additives may be selected according to different uses, and the commonly used additives are as follows: (1) curing agent; (2) modifier; (3) filler; (4) diluent; (5) others. Among them, the curing agent is an indispensable additive. Whether it is used as a binder, a coating or a castable, a curing agent is added, otherwise the epoxy resin cannot be cured. Due to the different performance requirements, there are different requirements for epoxy resin and additives such as curing agents, modifiers, fillers and diluents. Now, their selection methods are introduced as follows: (1) Selective use of epoxy resin For the choice of adhesive, it is best to use a medium epoxy resin (0.25-0.45) resin, such as 6101.634; It is good to use a resin with a high epoxy value (>0.40), such as 618.6101; a low epoxy value is generally used for coatings. (The mechanical strength of the epoxy resin is too high, but it is brittle; the epoxy value is medium. The strength is good at high and low temperatures; the low epoxy resin has lower strength at high temperature. Because the strength is related to the degree of cross-linking, the epoxy value is high after curing, the cross-linking degree is also high, and the epoxy value is low after curing. The degree is also low, so it causes a difference in strength.
The operation requirements do not need high temperature resistance, and the strength requirement is not large. It is hoped that the epoxy resin can be dried quickly and is not easy to be lost. The resin with lower epoxy value can be selected. If the permeability is good, the strength is better, and the epoxy value can be selected. Higher resin.
Curing agent selection
1. Type of curing agent:
Commonly used epoxy resin curing agents are fatty amines, alicyclic amines, aromatic amines, polyamides, acid anhydrides, resins, and tertiary amines. In addition, ultraviolet light or light can also cure the epoxy resin under the action of a photoinitiator. An amine curing agent is generally used for curing at room temperature or low temperature, and an acid anhydride and an aromatic curing agent are commonly used for heating and curing.
The epoxy value is the most important indicator for identifying the quality of epoxy resin. The type division of epoxy resin is distinguished according to the difference of epoxy value. The epoxy value means the number of gram equivalents of the epoxy group contained in 100 g of the resin.
Epoxy resin raw material
2. Curing agent dosage
(1) When the amine is used as a crosslinking agent, the following formula is calculated:
Amine dosage = MG/Hn
In the formula:
M = amine molecular weight
Hn=number of active hydrogen
G = epoxy value (number of epoxy equivalents per 100 grams of epoxy resin)
The range of change is no more than 10-20%, and if cured with an excess of amine, the resin becomes brittle. If the amount is too small, the curing is not perfect.
(2) When using an acid anhydride, the following formula is used:
The amount of anhydride = MG (0.6 ~ 1) / 100 in the formula:
M = acid anhydride molecular weight
G = epoxy value (0.6~1) is the experimental coefficient
3. The principle of selecting a curing agent: the curing agent has a great influence on the performance of the epoxy resin, and is generally selected according to the following points.
(1), from the performance requirements: some require high temperature resistance, some require good flexibility, and some require good corrosion resistance, then choose the appropriate curing agent according to different requirements.
(2), from the curing method: some products can not be heated, you can not choose a heat curing curing agent.
(3), from the application period: the so-called applicable period, refers to the time when the epoxy resin is added to the curing agent from the time when it can not be used. For long-term application, acid anhydrides or latent curing agents are generally used.
(4), from the choice of safety: generally requires less toxicity, easy to safe production.
(5), choose from the cost.
(III) Selection of modifiers
The role of the modifier is to improve the flexibility, shear resistance, bending resistance, impact resistance and insulation properties of the epoxy resin. Common modifiers are:
(1) Polysulfide rubber: It can improve impact strength and peeling resistance.
(2) Polyamide resin: It can improve brittleness and improve bonding ability.
(3), polyvinyl alcohol tert-butyraldehyde: improve the impact resistance.
(4), nitrile rubber: improve the impact resistance.
(5), phenolic resin: can improve temperature and corrosion resistance.
(6), polyester resin: improve the impact resistance.
(7), urethane melamine resin: increase chemical resistance and strength.
(8) Furfural resin: Improve static bending performance and improve acid resistance.
(9), vinyl resin: improve the peeling resistance and impact strength.
(10) Isocyanate: reduces moisture permeability and increases water resistance.
(11) Silicone resin: Improve heat resistance.
(four), the choice of filler
The role of the filler is to improve some properties of the product, and to improve the heat dissipation conditions when the resin is cured. The use of the filler can also reduce the amount of epoxy resin and reduce the cost. Different fillers can be used depending on the application. The size is preferably less than 100 mesh, depending on the application. The commonly used fillers are as follows:
Filler name | effect |
Asbestos fiber, fiberglass | Increase toughness and impact resistance |
Quartz powder, porcelain powder, iron powder, cement, silicon carbide | Increase hardness |
Alumina, porcelain powder | Increase adhesion and increase mechanical strength |
Asbestos powder, silica gel powder, high temperature cement | Improve heat resistance |
Asbestos powder, quartz powder, stone powder | Reduce shrinkage |
Metal powder such as aluminum powder, copper powder and iron powder | Increase thermal conductivity, electrical conductivity |
Graphite powder, talcum powder, quartz powder | Improve wear resistance and lubrication performance |
Emery and other abrasives | Improve wear resistance |
Mica powder, porcelain powder, quartz powder | Increase insulation performance |
Various pigments, graphite | With color |
In addition, it has been reported that an appropriate amount (27-35%) of oxides of P, AS, Sb, Bi, Ge, Sn, and Pb is added to the resin to maintain adhesion under high heat and pressure.
(5), the choice of thinner
Its role is to reduce viscosity and improve the permeability of the resin. The diluent can be divided into two categories, inert and active, and the dosage is generally not more than 30%. Commonly used diluents are as follows:
Reactive diluent
name | Diglycidyl ether | Polyglycidyl ether | Propylene oxide butyl ether | Propylene oxide phenyl ether | Dipropylene oxide ethyl ether | Tripropylene oxide propyl ether |
Brand | 600 | 630 | 660 | 690 | 669 | 662 |
Dosage | ~30% | Ibid. | ~15% | Ibid. | Ibid. | Ibid. |
Remarks | Need to add more amount of curing agent | Ibid. | Ibid. | Ibid. | Ibid. | Ibid. |
Inert diluent
name | Xylene | Toluene | benzene | acetone |
Dosage | ~15% | Ibid. | Ibid. | Ibid. |
Remarks | No need to add more curing agent | Ibid. | Ibid. | Ibid. |
Material Composition The epoxy resin anticorrosive material is mainly composed of the following materials. One is epoxy resin, which is a general term for polymers containing epoxy groups. It is mainly used for media with less corrosive properties. It has outstanding alkali resistance and can withstand general acid (except hydrofluoric acid) corrosion. The demand for epoxy resin has been greatly reduced in the market. The main reason is that the unsaturated polyester resin has been rapidly developed and has many varieties. In the domestic market, the unsaturated polyester resin started late, so the epoxy resin is still It is one of the main resin varieties in the field of corrosion protection. The main characteristics of epoxy resin are high bonding strength, low shrinkage, high brittleness and high price. The temperature of the resin cured at room temperature does not exceed 80 °C. The second is the curing agent of epoxy resin, which has amines and acid anhydrides. , resin compounds and other major varieties, of which amine compounds are most commonly used, it can be divided into fatty amines, aromatic amines and modified amines, etc., due to ethylenediamine, m-phenylenediamine, xylylenediamine, poly Compounds such as amide and diethylenetriamine have higher toxicity and odor, so they are gradually replaced by new non-toxic and low-toxic curing agents (such as T31.590, C20, etc.). These curing agents are also suitable for wet base and even underwater. Can be cured, so it has attracted people's attention and praise; Third, thinner, epoxy resin is usually diluted with non-reactive diluents such as: ethanol, acetone, benzene, toluene, xylene, etc., two kinds of inactive diluent can be mixed Use, sometimes in order to reduce the shrinkage of the cured product, reduce porosity and cracking also use reactive diluents, such as propylene oxide butyl ether, propylene oxide phenyl ether, polyglycidyl ether, etc.; Fourth, plasticizer, increase Toughener The epoxy resin is less brittle, impact toughness, flexural strength and heat resistance after curing. Plasticizers and toughening agents are commonly used to increase the plasticity, improve the toughness, and improve the flexural strength and impact toughness of the resin. Fifth, fillers, powders, fine aggregates, coarse aggregates, and glass scales are collectively referred to as fillers. Adding appropriate fillers can reduce the cost of the products and improve their performance. The amount of fillers in the glue is generally the amount of resin. 20 to 40% by weight, the amount of addition can be more when preparing putty, generally 2 to 4 times the amount of resin, commonly used powder is quartz powder, porcelain powder, in addition to graphite powder, diabase Powder, talcum powder, mica powder, etc.
Edit this paragraph resin selection purpose for the choice of adhesive as the best choice of medium epoxy value (0.25-0.45) resin, such as 6101.634; for castables, it is best to use high epoxy (>0.40) resin, Such as 618.6101; generally used for coatings with low epoxy value (mechanical strength, epoxy resin value is too high, but the brittleness; the epoxy value is medium and high, the strength is good; the epoxy value is low When the temperature is high, the strength is poor. Because the strength is related to the degree of crosslinking, the epoxy value is high after curing, and the degree of crosslinking is also high. The epoxy value is low and the degree of crosslinking is low after curing, so that the difference in strength is caused.
The operation requirements do not need high temperature resistance, and the strength requirement is not large. It is hoped that the epoxy resin can be dried quickly and is not easy to be lost. The resin with lower epoxy value can be selected. If the permeability is good, the strength is better, and the epoxy value can be selected. Higher resin.
Edit this paragraph curing selection type introduction Common epoxy resin curing agent is fatty amine, alicyclic amine, aromatic amine, polyamide, acid anhydride, resin, tertiary amine, in addition to the role of photoinitiator UV or light can also ring The oxygen resin is cured. An amine curing agent is generally used for curing at room temperature or low temperature, and an acid anhydride and an aromatic curing agent are commonly used for heating and curing.
The epoxy value is the most important indicator for identifying the quality of epoxy resin. The type division of epoxy resin is distinguished according to the difference of epoxy value. The epoxy value means the number of gram equivalents of the epoxy group contained in 100 g of the resin.
Brief introduction of dosage (1) when the amine is used as a crosslinking agent
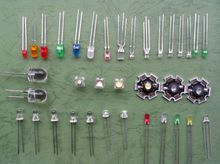
Epoxy LED package adhesive
Calculation:
Amine dosage = MG/Hn
In the formula:
M = amine molecular weight
Hn=number of active hydrogen
G = epoxy value (number of epoxy equivalents per 100 grams of epoxy resin)
The range of change is no more than 10-20%, and if cured with an excess of amine, the resin becomes brittle. If the amount is too small, the curing is not perfect.
(2) When using an acid anhydride, the following formula is used:
The amount of anhydride = MG (0.6 ~ 1) / 100 in the formula:
M = acid anhydride molecular weight
G = epoxy value (0.6 ~ 1) is the experimental coefficient selection principle. The curing agent has a great influence on the performance of the epoxy resin, generally selected according to the following points.
(1), from the performance requirements: some require high temperature resistance, some require good flexibility, and some require good corrosion resistance, then choose the appropriate curing agent according to different requirements.
(2), from the curing method: some products can not be heated, you can not choose a heat curing curing agent.
(3), from the application period: the so-called applicable period, refers to the time when the epoxy resin is added to the curing agent from the time when it can not be used. For long-term application, acid anhydrides or latent curing agents are generally used.
(4), from the choice of safety: generally requires less toxicity, easy to safe production.
(5), choose from the cost.
The function of the modified selection modifier is to improve the enthalpy, shear resistance, bending resistance, impact resistance and insulation performance of the epoxy resin. Common modifiers are:
(1) Polysulfide rubber: It can improve impact strength and peeling resistance.
(2) Polyamide resin: It can improve brittleness and improve bonding ability.
(3), polyvinyl alcohol tert-butyraldehyde: improve the impact resistance.
(4), nitrile rubber: improve the impact resistance.
(5), phenolic resin: can improve temperature and corrosion resistance.
(6), polyester resin: improve the impact resistance.
(7), urethane melamine resin: increase chemical resistance and strength.
(8) Furfural resin: Improve static bending performance and improve acid resistance.
(9), vinyl resin: improve the peeling resistance and impact strength.
(10) Isocyanate: reduces moisture permeability and increases water resistance.
(11) Silicone resin: Improve heat resistance.
The amount of polysulfide rubber and the like may be between 50 and 300%, and a curing agent is required; the amount of the polyamide resin and the phenolic resin is generally 50-100%, and the amount of the polyester resin is generally 20-30%, which can be no longer reinforced. The agent can also be added with a small amount of curing agent to promote the reaction faster.
Generally speaking, the more the amount of the modifier, the greater the flexibility, but the heat distortion temperature of the resin product is correspondingly decreased.
In order to improve the flexibility of the resin, a toughening agent such as dibutyl phthalate or dioctyl phthalate is also commonly used.
The filler is selected to improve the performance of the product and to improve the heat dissipation conditions of the resin. The use of the filler also reduces the amount of epoxy resin and reduces the cost. Different fillers can be used depending on the application. The size is preferably less than 100 mesh, depending on the application. The commonly used fillers are as follows:
Filler name effect
Asbestos fiber and glass fiber increase toughness and impact resistance
Quartz powder, porcelain powder, iron powder, cement, silicon carbide to increase hardness
Alumina and porcelain powder increase adhesion and increase mechanical strength
Asbestos powder, silica gel powder, high temperature cement improve heat resistance
Asbestos powder, quartz powder, stone powder reduce shrinkage
Metal powders such as aluminum powder, copper powder and iron powder increase thermal conductivity and electrical conductivity
Graphite powder, talc powder, quartz powder improve anti-wear performance and lubrication performance
Emery and other abrasives improve wear resistance
Mica powder, porcelain powder, quartz powder increase insulation performance
Various pigments, graphite have color
In addition, it has been reported that an appropriate amount (27-35%) of oxides of P, AS, Sb, Bi, Ge, Sn, and Pb is added to the resin to maintain adhesion under high heat and pressure.
The effect of dilution is to reduce the viscosity and improve the permeability of the resin. The diluent can be divided into two categories, inert and active, and the dosage is generally not more than 30%. Commonly used diluents are as follows:
Reactive diluent
Name grade purpose note
Diglycidyl ether 600 ~ 30% need to add more amount of curing agent
Polyglycidyl ether 630 Ibid.
Propylene oxide butyl ether 660 ~ 15%
Propylene oxide phenyl ether 690 Ibid.
Dipropylene oxide ethyl ether 669 Ibid.
Tripropylene oxide propyl ether 662 Ibid.
Inert diluent
Name usage note
Xylene ~15% no need to add more curing agent
Toluene is the same as above
Benzene is the same as above
Acetone is the same as above
Before adding the curing agent, all materials such as resin, curing agent, filler, modifier, thinner, etc. must be inspected, which should meet the following requirements:
(1), no moisture: the water-containing material should be dried first, and the solvent containing a small amount of water should be used as little as possible.
(2) Purity: The content of impurities other than water is preferably less than 1%. If the impurities are 5-25%, it can be used, but it is necessary to increase the percentage of the formula (the reagent grade is better when used in a small amount).
(3) Understand whether each material is invalid.
In the factory where the acceptance conditions are lacking, it is best to make a small sample test according to the formula before use.
Editing the curing phase of this section The operating time (also the working time or lifetime) is part of the curing time. After mixing, the resin/curing agent mixture is still liquid and can work and fit the application. In order to ensure reliable bonding, all construction and positioning work should be done during the curing operation time.
Entering the curing mixture begins to enter the solidified phase (also known as the ripening stage), at which point it begins to gel or "mutate." At this time, the epoxy does not work for a long time and may lose its viscosity. No interference can be made at this stage. It will turn into a hard rubber-like soft gel that you can press with your thumb.
Since the mixture is only partially cured at this point, the newly used epoxy resin can still be chemically linked to it, so the untreated surface can still be bonded or reacted. In any event, the ability to approach the cured mixture is to reduce the final cured epoxy mixture to a solidified stage of solidification, where it can be sanded and shaped. At this point you can't hold it with your thumb. At this point, the epoxy resin has about 90% of the final reaction strength, so you can remove the retaining clip and leave it at room temperature to keep several angels from solidifying.
At this time, the newly used epoxy resin cannot be chemically linked with it, so the epoxy surface must be properly pretreated, such as sanding, to obtain good bonding mechanical strength.
Edit this paragraph Application area Introduction Introduction The excellent physical and mechanical properties of epoxy resin, the bonding properties with various materials, and the flexibility of its use process are not available in other thermosetting plastics. Therefore, it can be used in coatings, composites, castings, adhesives, molded materials and injection molding materials, and is widely used in various fields of the national economy.
The use of epoxy resin in coatings accounts for a large proportion of coatings, and it can be made into various varieties with different characteristics and uses. Their commonalities:
1. Excellent chemical resistance, especially alkali resistance. 2. The paint film has strong adhesion, especially to metal.
3. Has good heat resistance and electrical insulation.
4. The paint film has good color retention.
However, the bisphenol A type epoxy resin coating has poor weather resistance, and the paint film is easy to be powdered and lost in the outdoor, and is not suitable for outdoor coatings and high decorative coatings. Therefore, epoxy resin coatings are mainly used as anticorrosive paints, metal primers, and insulating paints, but coatings made of heterocyclic and cycloaliphatic epoxy resins can be used outdoors.
Adhesive use epoxy resin is not good for non-polar plastics such as polyolefin, but also for various metal materials such as aluminum, steel, iron, copper; non-metallic materials such as glass, wood, concrete, etc.; and thermosetting Plastics such as phenolic, amino, unsaturated polyesters, etc. have excellent bonding properties, so they are known as universal adhesives. Epoxy adhesives are an important variety of structural adhesives.
The main use of epoxy resin adhesive is shown in Table l-1. Table l-2 and Table l-3.
表1-1 çŽ¯æ°§æ ‘è„‚èƒ¶ç²˜å‰‚çš„ä¸»è¦ç”¨é€”
Application field | è¢«ç²˜ææ–™ | 主è¦ç‰¹å¾ | 主è¦ç”¨é€” |
åœŸæœ¨å»ºç‘ | æ··å‡åœŸï¼Œæœ¨ï¼Œé‡‘属,玻璃,çƒå›ºæ€§å¡‘ | 低é»åº¦ï¼Œèƒ½åœ¨æ½®æ¹¿é¢ï¼ˆæˆ–æ°´ä¸ï¼‰å›ºåŒ–,低温固化性 | æ··å‡åœŸä¿®è¡¥ï¼ˆæ–°æ—§é¢çš„衔接),外墙裂ç¼ä¿®è¡¥ï¼ŒåµŒæ¿çš„粘结,下水é“管的连接,地æ¿ç²˜ç»“,建ç‘ç»“æž„åŠ å›ºã€‚ |
电å电器 | 金属ã€é™¶ç“·ï¼ŒçŽ»ç’ƒï¼ŒFRPç‰åŠ¿å›ºæ€§å¡‘æ–™ | 电ç»ç¼˜æ€§ã€è€æ¹¿æ€§ï¼Œè€çƒå†²å‡»æ€§ï¼Œè€çƒæ€§ï¼Œä½Žè…蚀性 | 电å元件,集æˆç”µè·¯ï¼Œæ¶²æ™¶å±ï¼Œå…‰ç›˜ï¼Œæ‰¬å£°å™¨ï¼Œç£å¤´ï¼Œé“èŠ¯ï¼Œç”µæ± ç›’ï¼ŒæŠ›ç‰©é¢å¤©çº¿ï¼Œå°åˆ¶ç”µè·¯æ¿ |
航天航空 | 金属,çƒå›ºæ€§å¡‘料,FRP(纤维增强塑料) | è€çƒï¼Œè€å†²å‡»ï¼Œè€æ¹¿æ€§ï¼Œè€ç–²åŠ³ï¼Œè€è¾å°„线 | åŒç§é‡‘属ã€å¼‚ç§é‡‘属的粘接,蜂çªèŠ¯å’Œé‡‘å±žçš„ç²˜æŽ¥ï¼Œå¤åˆææ–™ï¼Œé…电盘的粘接 |
汽车机械 | 金属,çƒå›ºæ€§å¡‘料,FRP | è€æ¹¿æ€§ï¼Œé˜²é”ˆï¼Œæ²¹é¢ç²˜æŽ¥ï¼Œè€ç£¨è€ä¹…性(疲劳特性) | 车身粘结,薄钢æ¿è¡¥å¼ºï¼ŒFRP粘结,机械结构的修å¤ã€å®‰è£… |
ä½“è‚²ç”¨å“ | 金属,木,玻璃,çƒå›ºæ€§å¡‘料,FRP | è€ä¹…性,è€å†²å‡»æ€§ | 滑雪æ¿ï¼Œé«˜å°”å¤«çƒæ†ï¼Œç½‘çƒæ‹ |
other | 金属,玻璃,陶瓷 | ä½Žæ¯’æ€§ï¼Œä¸æ³›é»„ | 文物修补,家åºç”¨ |
表1-2 环氧胶粘剂在土木建ç‘上的主è¦ç”¨é€”
工程类别 | 粘接对象 | 典型用途 | 主è¦ç»„æˆ |
基础结构 | 岩石—岩石 金属—石或混å‡åœŸ 金属—混å‡åœŸ 金属—金属 | ç–æ¾å²©å±‚的补强ã€åŸºç¡€åŠ å›ºã€é¢„åŸ‹èžºæ “ã€åº•脚ç‰ï¼ŒæŸ±åã€æ¡©å¤´ã€æŽ¥é•¿ã€æ‚¬è‡‚æ¢åŠ ç²—ã€æ¡¥æ¢åŠ å›ºã€è·¯é¢è®¾æ–½æ•·è®¾ | 环氧—稀释剂—改性胺 环氧—填料—改性胺 åŒé…šSçŽ¯æ°§â€”ç¼©æ°´ç”˜æ²¹èƒºæ ‘è„‚â€”ä¸åŸºæ©¡èƒ¶â€”改性胺 |
åœ°é¢ | ç“·ã€èŠ±å²—çŸ³â€”æ··å‡åœŸ 金属—混å‡åœŸ ç ‚çŸ³â€”æ··å‡åœŸ PVC—橡胶—金属 | è€è…蚀地åªåˆ¶é€ ä¸ç²˜ç»“æž„åŠå‹¾ç¼ï¼›åœ°é¢é˜²æ»‘和美化ã€å‡€åŒ–;地æ¿çš„铺设 | 环氧—填料—改性胺 环氧—èšç¡«æ©¡èƒ¶â€”改性胺 丙烯酸酯—环氧共èšä¹³æ¶² |
ç»´ä¿® | æ··å‡åœŸã€é’¢ç‹ã€ç°æµ† | å ¤åã€é—¸é—¨ã€å»ºç‘物的裂ç¼ã€ç¼ºæŸã€èµ·å£³çš„ä¿®å¤ï¼Œæ–°æ—§æ°´æ³¥ç²˜æŽ¥ | 环氧—糖醇—改性胺 环氧—沥é’—改性胺 环氧—活性石ç°â€”改性胺 |
装璜 | 金属ã€çŽ»ç’ƒã€å¤§ç†çŸ³ã€ç“·ç –有机玻璃ã€èšç¢³é…¸é…¯ | 墙é¢ã€é—¨é¢ã€æ‹›ç‰Œã€å¹¿å‘Šç‰Œçš„安装和装潢 | çŽ¯æ°§â€”èšæ°¯é…¯ 环氧—有机硅橡胶 |
给排水 | é‡‘å±žã€æ··å‡åœŸ | 管é“ã€æ°´æ¸ è¡¬é‡Œï¼Œç®¡æŽ¥å¤´å¯†å° | 环氧—改性芳香胺 |
表1-3 环氧胶粘剂在汽车上的主è¦ç”¨é€”
use | è¢«ç²˜ææ–™ | ç²˜ç»“éƒ¨ä½ | å…¸åž‹ç»„æˆ |
å·è¾¹ã€ç‚¹ç„Š | é’¢æ¿â€”é’¢æ¿ | å‘动机罩ã€é—¨ã€è¡ŒæŽç®±åº• | å•组分ã€çŽ¯æ°§â€”èšæ°¯é…¯ |
补强 | é’¢æ¿â€”FRP é’¢æ¿â€”呿³¡ææ–™ | é—¨ä¸éƒ¨ 门把手 | 环氧—å硼酸三甲酯 环氧—èšé…°èƒº |
结构粘接 | 碳ã€çŽ»ç’ƒçº¤ç»´ï¼Œé’¢ï¼Œç”Ÿé“ | 驱动轴ã€åˆ¹è½¦ç‰‡ | å•组分环氧原浆料 |
ç²˜ç»“å¯†å° | FRPâ€”æ¶‚è£…é’¢æ¿ | 车顶—窗框 | 环氧—èšç¡«æ©¡èƒ¶ |
装饰粘接 | èšä¸™çƒ¯é…¸é…¯â€”èšä¸™çƒ¯ | åŽèƒŒç¯åº§ | æ”¹æ€§çŽ¯æ°§æ ‘è„‚ |
2.广泛用于装有电å元件和线路的器件的çŒå°ç»ç¼˜ã€‚å·²æˆä¸ºç”µå工业ä¸å¯ç¼ºå°‘çš„é‡è¦ç»ç¼˜ææ–™ã€‚
3.电å级环氧模塑料用于åŠå¯¼ä½“元器件的塑å°ã€‚è¿‘å¹´æ¥å‘展æžå¿«ã€‚由于它的性能优越,大有å–ä»£ä¼ ç»Ÿçš„é‡‘å±žã€é™¶ç“·å’ŒçŽ»ç’ƒå°è£…的趋势。
4.环氧层压塑料在电åã€ç”µå™¨é¢†åŸŸåº”用甚广。其ä¸çŽ¯æ°§è¦†é“œæ¿çš„å‘展尤其迅速,已æˆä¸ºç”µ
åå·¥ä¸šçš„åŸºç¡€ææ–™ä¹‹ä¸€ã€‚
æ¤å¤–,环氧ç»ç¼˜æ¶‚æ–™ã€ç»ç¼˜èƒ¶ç²˜å‰‚和电胶粘剂也有大é‡åº”用。
工程塑料环氧工程塑料主è¦åŒ…括用于高压æˆåž‹çš„环氧模塑料和环氧层压塑料,以åŠçŽ¯æ°§æ³¡æ²«å¡‘æ–™ã€‚çŽ¯æ°§å·¥ç¨‹å¡‘æ–™ä¹Ÿå¯ä»¥çœ‹ä½œæ˜¯
Fruit Carrier Oil
The Fruit Oil is made from truly natural, therapeutic ingredients that protect, moisturize, and nourish your skin.
Such as below.
Aloe Oil ,Olive oil,Pine nuts oil,Shea Butter Oil,Cucumber oil,Sweet Almond Oil,Evening primrose oil,Coconut oil,Palm oil,Wheat germ
oil,Soybean oil,Borage Oil, Jojoba Oil ,Rosehip Oil, Argan Oil
Please contact us for more details.
Shea Butter Oil,Sweet Almond Oil,Aloe Oil,Pine Nut Oil
Jiangxi Global Natural Spice Co., Ltd. , http://www.chessentialoil.com