1. Mineral raw materials, auxiliary materials and quality requirements
The choice of raw and auxiliary materials is mainly based on the customer's requirements for product quality and the amount of graphite deposits. If the end user needs high tensile strength, low ash, low heat and weight loss graphite products, then coarse-grained, high-purity raw materials should be used. For example, type 3299, if the customer does not require high tensile strength, only a certain rebound rate is required, then fine-grained, low-purity grades such as 5099 are used. However, the current reserves of 3299 and other models are decreasing. The mining difficulty is getting bigger and bigger, the cost is getting higher and higher, and the development of fine-grained graphite raw materials has become an inevitable trend of some manufacturers.
2. Production process, formulation, technology and main equipment
Process: flake graphite + oxidant---reaction tank (soaking, stirring)---sink (cleaning)---centrifuge
(Dehydration)---Oven (drying)---High temperature furnace (expansion)---Graphite worm---Mold (forming to finished product)
Technical Note: The purpose of immersion is to form a layer compound or graphite salt between the flake graphite layers. The key here is the formulation of the oxidant. The most typical formula is: 90% (by volume) concentrated sulfuric acid + 10% (volume ratio) The concentrated nitric acid line is formed into an oxidant, and the ratio of the oxidant to the graphite is preferably soaked in the graphite. The soaking process can be slowly stirred to improve the soaking effect; the formulation is characterized in that the produced graphite product has good flexibility and tensile strength. High strength, but there must be residual sulfur (usually the purpose of washing to remove the oxidant on the graphite surface of the phosphorus flakes, the washing time and the amount of water can generally reach the pH value of the graphite surface of the phosphor flakes to about 3, and then dehydrated with a centrifuge, the centrifuge does not Too high a requirement, generally use an ordinary industrial centrifuge, which is lined with a layer of wire mesh to prevent the graphite phosphor film from flying out.
After dehydration, it is sent to the oven for drying. The design of the oven is mainly at the drying temperature. Generally, it is about 100 °C. If the temperature is too low, the drying time is too long. If the temperature is too high, it will partially oxidize and reduce the yield. Natural sunlight can also be dried, and the degree of drying is not suitable for the graphite flake graphite.
The dried graphite can be sent to the high temperature furnace for expansion. The key of the expansion process is the furnace temperature and the feeding amount. Generally, the furnace temperature of about 1000 °C is used to let the dried acidified particles pass through the furnace, and instantaneously, due to the interlayer oxidant and a small amount. The water vaporizes at high temperature to promote the graphite particles to expand 80-300 times in the C-axis direction. The feed amount is also related to the power of the furnace. If the furnace temperature drops sharply or the unexpanded particles are found at the exit of the furnace, the feed rate should be adjusted.
(3) Corrosion resistance: In addition to strong oxidizing medium such as concentrated sulfuric acid, aqua regia, concentrated nitric acid, expanded graphite material can be exposed to acid, alkali salt and organic solvent for a long time.
(4) Radiation resistance: can be used in the atomic energy industry
(5) Good conductor of thermoelectricity
(6) Good impermeability to gases and liquids
For example, an expanded graphite sheet with a thickness of 1.75 mm has an oxidation leakage rate of only 1.3 to 2 x 10-5 cc/cm2.
4. Main uses and application fields
Fill the seal in the stuffing box of the static seal of the valve, pump, etc.
Sealing gaskets in flanges, blind plates, heat exchangers and cylinders.
There are also many forms of packing seals, such as packing rings, packing, combined seals, and mud seals.
Flange gaskets are also available in many forms, such as pure graphite gaskets, high-strength gaskets for metal-sealed spurs, wound gaskets, and corrugated composite gaskets.
Recommended Products:
This article is reproduced from: http://
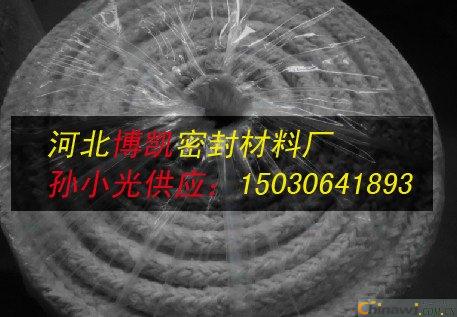
Product categories of Double Layer Roll Forming Machine,we are specialized
manufacturers from China, Double Layer Roll Forming Machine,sheet rollforming machine,
suppliers/factory,wholesele high-quality product of Double Layer Roll Forming Machine,
R & D and manufacturing , we have perfect after-sales service and technical support . Look forward
to your cooperation !
Double Layer Roll Forming Machine
Double Layer Roll Forming Machine,Double Layer Roll Forming Equipment,Double Layer Roll Making Machine,Double Layer Roll Forming Machinery
BOTOU HUATONG CORRUGATED MACHINERY MANUFACTURING CO.,LTD , http://www.htrollforming.com